This week, there were two attempts to launch the first mission of the Artemis program, also the first flight of the SLS rocket. Both attempts were aborted during the countdown, which raised many questions. In this article, the first in our series on the Artemis program, we’ll discuss what happened, what the future of the mission will be and, above all, what it means to cancel launch attempts.
The launch attempts
The first attempt, on August 29th, was delayed by 1 hour in order to wait for the weather conditions to improve, because at the time originally scheduled the chance of lightning was above the limit (20%). The delayed start meant that there was 1 hour less to examine and try to solve the problems that arose later. After the start of fueling, there was a small leak in the main stage disconnects, detected by the hydrogen sensors installed on the platform. These leaks occurred during slow fueling, in which the fuel is pumped slowly so that the components gradually cool down. After stopping the refueling, letting the seals warm up and restarting the slow refueling, these leaks stopped. Then came the engine cooling phase, carried out by letting fuel and oxidizer flow through them, so that engine components don’t suffer from the thermal shock of a sudden high flow of cryogenic liquids (-183°C for oxygen, -253°C for hydrogen) and to prevent the liquids from boiling when they encounter “hot” engine components (ambient temperature). 3 of the 4 main stage engines were cooling as expected, but engine number 3 was not. After a long time trying to solve the problem and the start of a small leak in the interstage exhaust valve, the team considered that it would not be possible to solve the temperature of engine 3 in time, and the attempt was canceled about 4 hours before the end of the countdown. It was also noted that the weather conditions were difficult on the day, only in the last half hour of the 2-hour window would it have been possible to launch, because of thunderstorms in the area.
Analysis of all the data from multiple sensors in various locations on the rocket indicated that the problem was possibly with the temperature sensor, as other sensors around it indicated correct temperatures. For the second attempt, on September 3, more time was allocated for cooling, to give more chance to better analyze the behavior of the engines and try other procedures if necessary. But it wasn’t possible to get to the stage of cooling the engines. After the start of the fast refueling (after the slow refueling, where there were problems on the 29th), a large leak was observed in the main stage’s 8-inch disconnect. This was much larger than all those detected in other tests and launch attempts. After 3 attempts to seal the leak with heating and cooling cycles and by changing the pumping rate, with the leak reocurring all 3 times, the team considered that it would not be possible to resolve the leak in time to launch within the window, and the launch was canceled about 3 hours before the end of the countdown.
These quick disconnects are critical components, making the connection between the launch pad pipes and the rocket pipes, and must at the moment of launch separate and completely seal off the rocket side. The process has to be quick because it takes place in the last few moments before the rocket starts to ascend, because up until this point the rocket is still receiving fuel and oxidizer through these pipes. Why not stop refueling earlier? Because the cryogenic propellants spend all their time boiling and evaporating inside the tanks, with the excess vapor escaping through valves (to keep the pressure under control), so it is necessary to keep refueling continuously until launch. And it is notoriously difficult to get good seals on joints that need disconnecting (non-permanent joints) in hydrogen pipes, because hydrogen gas, having the smallest molecules, leaks very easily. This is one of the reasons why many rockets use RP-1 (rocket propellant 1, essentially kerosene), which is less efficient but much easier to handle than cryogenic hydrogen. This contrasts to SpaceX’s Falcon 9 rockets only using cryogenic oxygen (the fuel is RP-1, which can be left at room temperature) and do not use rapid disconnects. And for this reason heavier Falcon 9 launches are often canceled due to minor delays, because the launch window is instantaneous: they can’t delay the launch time because of the loss of oxygen evaporating from the time of disconnection.
Is this normal?
Yes, completely normal. Artemis I is the first flight of the SLS rocket and it’s a test flight – so there’s no crew inside. Although all the components have been tested individually in simulated situations and there are complex models to predict how everything will work, it is necessary to test the whole system, integrated, in a real flight. And this isn’t “just” about testing whether the rocket works as built. It includes testing the procedures for using it. Unlike say, a car, one doesn’t just press a button to start it. There is a huge and complex set of procedures required for the launch to take place, each with many parameters to choose from. For example: how much to open which valves, for how long, when to fill the cryogenic fuel and oxidizer tanks, doing lots of tests and controlling the temperatures and pressures in different components so as not to exceed safety limits or cause damage or leaks (by cooling too quickly, for example). All these procedures were defined in advance according to previous tests and simulations, but it is in tests like this that one learns what works and what needs to be changed.
That’s why the countdown starts 46 hours before launch, with the most intense part in the last 8 hours, when the cryogenic tanks are filled. Cancellations of a launch attempt(scrubs) for technical reasons, like these two for Artemis I, occur when at some point in the countdown the engineers assess that there is something that needs to be changed and there won’t be time to fix or change it before the end of the launch window (which, in the case of these two attempts, was 2 hours). Canceling an attempt doesn’t mean that something is seriously wrong, nor does it indicate incompetence or that they won’t be able to launch. On the contrary, the most reliable operators are those who monitor many variables in great detail during the countdown and don’t hesitate to cancel if something is outside the right parameters. When this doesn’t happen, either because there isn’t enough monitoring or because there is a “we have to launch anyway” attitude, there is a higher risk of a serious mission failure, including loss of vehicle, cargo and even lives.
In the case of NASA, a major change in attitude was the main result of the investigation into the Space Shuttle Challenger accident, which in 1986 exploded during launch, with the loss of the 7 astronauts on board. The immediate cause of the accident was launching when it was too cold: the rubber seals (O-rings) that seal the joints between the segments of the solid boosters froze and thus lost their elasticity, failing to contain the flames of combustion taking place inside the rocket. But much more fundamentally, the cause of the accident was the pressure to launch without delaying the year’s dense launch schedule, which led to engineers’ warnings about the low temperature being ignored. The investigation led to a major change in policy, placing much more emphasis on increasing monitoring, testing and simulations of all critical systems before launch and paying close attention if any parameters were out of line or outside the known domains of operation. This can be summed up with the current saying always repeated to operators: “no one will remember a canceled launch, but everyone will always remember if it launches and explodes”. Or, as SpaceX often repeats after each new Starship explosion: “that’s why we test”. All rockets (current and past, without exception) from any company or agency have had many launch attempts postponed or canceled, for any number of reasons. But scrubs are so normal and frequent that they don’t usually make the news. Artemis I has gained so much publicity now because of the great expectation for the return to the Moon. But just like the attempts to launch the James Webb Space Telescope in 2021, these cancellations will soon be forgotten.
Shortly after the Space Shuttle return to flight, there was a great example of how the new policy was applied and ensured safety: you probably remember the Challenger explosion in 1986, but do you remember the “summer of hydrogen” in 1990? It was a situation that lasted 7 months, involving all 3 Space Shuttles in existence at the time. Don’t remember? Hardly anyone today even knows it happened. Because launch attempts were canceled and then all 3 vehicles made their flights without any problems:
The “summer of hydrogen”

The year 1990 was set to be extremely busy for the Shuttle, with 9 flights between the 3 vehicles that existed at the time (Columbia, Discovery and Atlantis). In May, Columbia was on the pad being fueled for its launch and a small leak was detected in the disconnect between the vehicle and the pad, at the start of rapid fueling, 4 hours before launch. On examining the problem, a much larger leak was detected, coming from inside Columbia, which could not be solved on the spot. The launch was canceled. 6 days later, a refueling test showed that it would not be possible to solve the problem on the platform, the Shuttle was taken back to the Vehicle Assembly Building (VAB), from where it was removed from the stack (the orbiter, external tank and the two boosters) to be opened and examined. The two sides of the disconnects between the Space Shuttle and the external tank, which join 43 cm diameter tubes through which the hydrogen that powers the 3 engines passes, were replaced. While this was going on, back in July, Space Shuttle Atlantis was on the platform for its launch. A refueling test was carried out… and the same type of leak was detected. More instruments were added to better measure conditions and a new test was carried out 12 days later. A leak was observed in the same region. Atlantis would also have to be taken back to the VAB and unstacked. In August, Columbia was taken back to the pad for a September launch, on the way passing Atlantis, which was being taken back to the VAB:
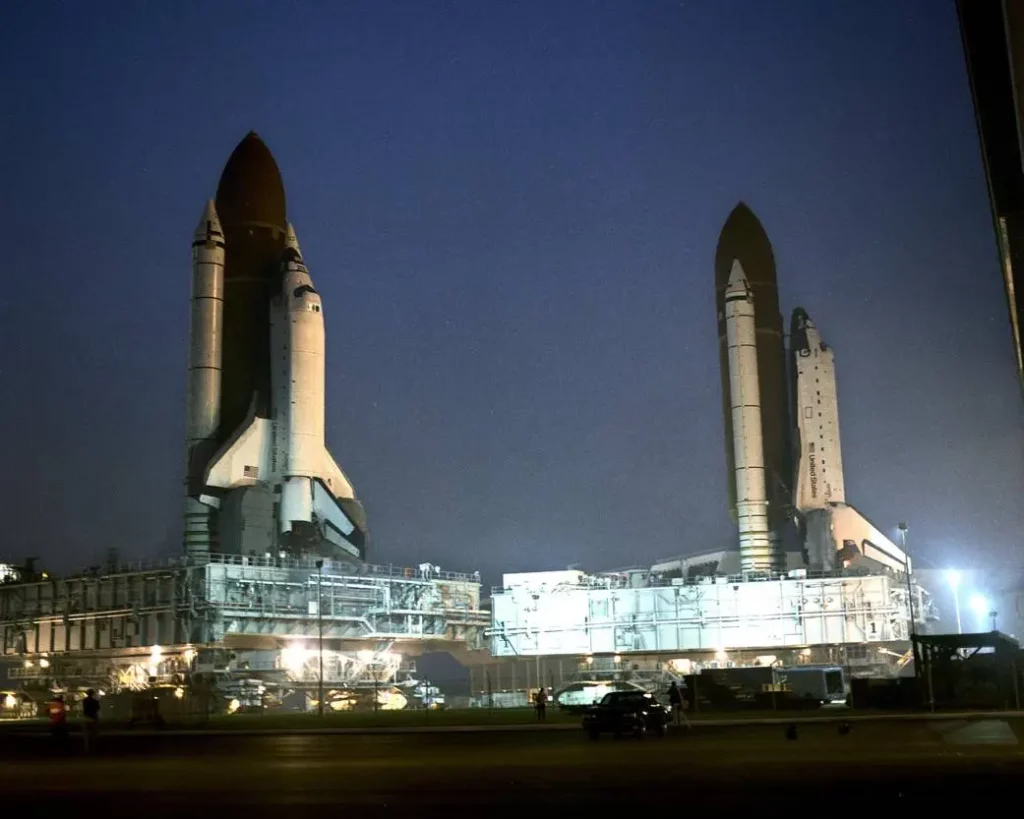
Despite having the same symptoms, it was identified that the cause of the leaks was different: on Columbia it was the seal on the Space Shuttle’s quick disconnect cover. On Atlantis, it was the incorrect torque applied to a flange on the disconnect. With Columbia back on the pad, after another delay of a few days to solve an electronic problem with the payload (the ASTRO-1 satellite), the new fueling began. And a new large hydrogen leak was detected. New sensors indicated that the original leak no longer existed; this was another leak, inside Columbia’s engine compartment. While they were trying to solve these problems, the launch of Space Shuttle Discovery was approaching, this one with a narrow and critical window, as it was carrying the Ulysses probe that was going to observe the Sun. 3 hydrogen circulation pumps and a seal were changed on the Columbia, still on the pad, to try to launch again 13 days later. On this new attempt… again a hydrogen leak. With Discovery’s critical launch approaching, Columbia couldn’t wait any longer on the pad: back to the VAB, for the second time. A large team of engineers from various NASA centers was assembled to work intensively on the problem. Meanwhile, Discovery launched without any problems on October 6. At the end of October, Columbia finally passed a refueling test without any problems. And soon after, on November 17, Atlantis, back on the launch pad after repairs, also flew without a hitch. December 2 arrived, more than 6 months after the original launch date, and Columbia finally flew, without any problems. It was identified that the source of many of Columbia’s leaks was residuals after a cleaning operation carried out earlier in the year, combined with the fact that the focus of inspections at the time was on the disconnects and not enough inspections and tests were carried out on the engine joints, a procedure that has been changed to avoid repetitions of these problems in the future.
After all those months of canceled launch attempts, tests, trips back to the VAB and repairs, all three Space Shuttles at the time (Endeavour was being built) successfully completed their missions. And today nobody remembers those delays. But one can imagine what it would have been like if Twitter had existed at the time: countless posts about “disaster”, “NASA failing”, “NASA can’t go into space” or “the future is Orbital Sciences Corporation’s revolutionary rocket” (Orbital Sciences’ Pegasus rocket, the first to be developed by a private company, had just made its maiden flight).
Read more about the history of the “summer of hydrogen” in these articles:
The future
As there won’t be time to examine the causes of the leak before the end of the current period (25) on Tuesday, the next attempt would be in period 26 (Sept. 19-Oct. 4) or 27 (Oct. 17-31). Period 26 seems unlikely, as it exceeds the 25-day limit on the launch pad given by flight safety officials, due to there being no tests of the flight termination system (“self-destruct”) for longer periods. It is possible that, by reviewing the system’s test data, an extension will be granted, but it is not certain that there will be one, nor does it seem likely. This implies the need to take the SLS back to the Vehicle Assembly Building (VAB) to review the termination system. It is also possible that other systems in the many payloads (see more about them in our article on Artemis I) will need to be serviced, such as changing batteries or other consumables. In addition, at the end of September and beginning of October there is a conflict with SpaceX’s launch of the Crew 5 mission to the Space Station (currently scheduled for October 3, after many delays).
The next steps to resolve the leaks are to undo the suspect connections, change the seals and reconnect them. The choice was made to do them on the launch pad. It’s a more difficult place to work and requires building an eclosure around the work area, but it has the advantage of being able to do cryogenic tests, which are more informative – because a frequent cause of leaks is uneven temperature changes on two sides of a joint, which cause different components to contract differently. If the operation were carried out in the VAB (another option that was considered) the tests would be limited to higher temperatures. In addition, a detailed analysis of the events during this week’s two attempts will be carried out, combined with comparisons with the component tests previously carried out at NASA’s Stennis Center (before the rocket was assembled), data from Space Shuttle flights and analysis of the components removed from the SLS, to identify what changes in procedures could help prevent further leaks.
Update (November 15): During the passage of Hurricane Nicole, the winds, although strong (gusts of up to 160 km/h at the height of the top of the rocket) never exceeded the operating limits. And it’s worth remembering that the operating limits were chosen at the level of 75% of the safety limit, leaving 25% margin. And the safety limit, in turn, is 70% of the vehicle’s structural limit, leaving a further 30% margin. There was only minor damage found, none of it structural, the most relevant being the loss of part of a coating called RTL at the splice of the Orion coating with the service module, but the result of the analyses is that the effect (on drag and heating) should be small, as is the risk of other pieces coming loose and causing damage. In addition, there was only one set of cables that fell off the support truss, which have now been replaced, and an electrical connection on a sensor used to start the auxiliary power unit (APU) before launch presenting more noise than normal, but is not considered an impediment as it is redundant.
Update (November 8): After being prepared for launch and taken back to the pad for launch on November 14, the launch has been postponed because of Hurricane Nicole. This time, because the forecast is for winds below the safety limit, the rocket will endure the hurricane on the platform, without being taken back to the VAB. The next attempt is currently scheduled for November 16, if there are no major difficulties with the return of employees after the hurricane.
Update (September 26): After analyzing the latest weather forecasts, it was decided this morning that the SLS will be moved back inside the VAB, due to Hurricane Ian. The move will begin at 11pm tonight (local time), and should end tomorrow, allowing time for the rocket to be protected and for employees to take leave and take care of their hurricane precautions. The region already has a preventive state of emergency declared and the population is being instructed to learn evacuation routes, pack and have supplies, including water, for at least 3 days.
Update (September 24): After the successful fueling test on the 21st, the launch on the 27th will probably be postponed due to tropical storm Ian, which is approaching Florida. The current forecast indicates that it will be necessary, in addition to postponing, to move the SLS back into the VAB, where it is protected and to allow more employees to leave early, which may be necessary, especially if there are evacuations. The final decision will be made tomorrow (the 25th), after analyzing the new weather forecasts.
Update (September 12): Work has already begun on undoing the connections to replace the seals. A cryogenic supply test is expected to be carried out on September 21. If this test indicates that all the problems have been solved, there are two possible launch windows in period 26: September 27, with a possible alternative on October 2, with the SLS remaining on the platform at all times, without returning to the VAB. These are the possible dates so as not to conflict with the impact of the DART mission to an asteroid on the 27th (which will occupy the Deep Space Network, which Artemis needs to communicate with Earth from the day after launch), and the launch of the Crew 5 manned mission to the Space Station. But the use of these windows still depends on the safety officer approving the request to extend the use period of the flight termination system’s batteries. If they have to be replaced, the rocket will have to be taken back to the VAB, which would push the next launch to period 27, at the end of October.
In the words of NASA administrator Bill Nelson: “there is no political pressure to launch anyway and if there was, I would be strongly rejecting it” and “we will launch when there is confidence that everything is right”. He also recalled that when he went into space, on the Space Shuttle, there were 4 canceled launch attempts, but on the fifth attempt everything worked and it was a very successful mission – even before the Challenger accident, which occurred just 10 days later.
Find out more at
Our article on Artemis I
How the launch went
Our article on the SLS rocket
Our article on the Artemis Program
This post is also available in:
Português