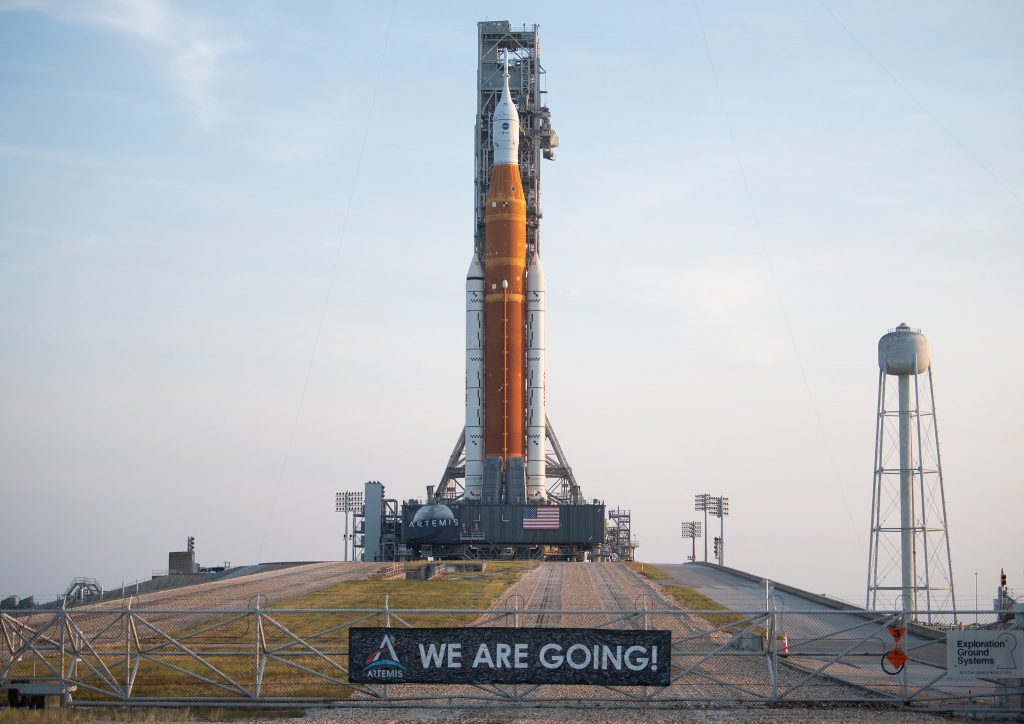
The first launch of the world’s largest rocket, the SLS – Space Launch System, is scheduled for August 29.
Update (August 29): The team is examining why the exhaust valve on one of the engines isn’t at the right temperature, and has concluded that there won’t be time to fix it in time for today’s launch. Next opportunity: Friday, September 2nd.
The rocket is already on Launch Pad 39B at NASA’s Kennedy Space Center. On August 22, the Flight Readiness Review was completed and the rocket was approved for launch on August 29 (“Go for launch”). The 2-hour launch window begins at 07:33 EST. The official live broadcast begins 2 hours earlier, at 05:30:
What will it be used for?
With the coincidence of the great expectation for the first flight of the SLS and the great expectation for the first mission to the Moon with the Artemis program, it is common for the two to be confused. But they are different projects: Artemis is the program that will take humans back to the Moon for the first time since 1972, this time to establish an orbital station and a permanent base (see more in our article). To be able to carry the large payloads required, the Artemis program will use the SLS rocket.
But the SLS doesn’t just exist for Artemis. It is the current super heavy vehicle for all missions in the coming decades that require carrying very large payloads or at very high speeds: the capacity of a rocket determines how much kinetic energy it can give to the payload, which can be a very massive payload on a relatively low-speed trajectory or a low-mass payload at high speed. This includes the missions to the Moon with the Artemis program, the first manned missions to Mars and large unmanned vehicles to very distant destinations, such as the one that would land on Jupiter’s moon Europa – noting that it’s not the distance itself that requires a larger rocket, but the larger rocket makes it possible to launch at a higher speed, cutting several years off the travel time to the Solar System beyond Mars.
The origins of the SLS come from earlier programs: in the 2000s, NASA’s super heavy vehicle was the Space Shuttle, which was capable of taking a large crew into low Earth orbit in the cabin (up to 11 astronauts, plus up to 24 ton in its cargo bay) and was being used to build the International Space Station and maintain the Hubble Space Telescope. As a comparison, SpaceX’s Crew Dragon vehicle only carries up to 4 crew members on short flights and a Space Shuttle had the volume and capacity in its cargo compartment to carry 2 entire Crew Dragons, with their trunks. With its imminent retirement in 2011, the new strategy adopted by NASA was to delegate what would have been simple missions (small cargo or manned capsules to low orbit) to private companies and create a new NASA vehicle for very large loads, at a size which only operated at the time of the Apollo program (the Saturn V). To save time, cost and risk in development, derivative technologies and even equipment from the two previous major programs, Apollo and the Space Shuttle, would be adopted. The first result was the Constellation program, proposed in 2004, which would have two rocket models, the Ares V (for large unmanned payloads) and the Ares I to only carry the Orion capsule (to be developed) to rendezvous in low orbit with other spacecraft launched by the Ares V (such as a service module or landing on the Moon). In 2010, Congress and the President decided to cancel the Constellation program and in the 2011 budget a reformulation of the concept was proposed, which was then the SLS.
What is the SLS like?
As legacy from Constellation, SLS adopted the use of concepts and equipment from Apollo, the Space Shuttle and the Delta IV rocket, keeping the Orion spacecraft as a manned compartment for journeys long enough to reach the Moon. But instead of different rockets for cargo and crew, it’s a bigger rocket, carrying both at the same time. The elements of the SLS can be roughly seen as: a capsule for the crew, derived from the Apollo design, on top of all the propulsion elements of the Space Shuttle (the external tank, the solid boosters and the engines, but without the orbiter). On top goes a second stage, derived from the second stage of the Delta IV rocket. Over three generations, the SLS will undergo changes, increasing its capacity: Block 1 (70 tons capacity for low orbit), Block 1B (105 tons) and Block 2 (130 tons):

1. Core Stage
The main stage is derived directly from Space Shuttle propulsion. It is the orange body containing the hydrogen and oxygen tanks. Unlike the Space Shuttle tank, the SLS tank contains engines: 4 RS-25D engines, also known as SSME – Space Shuttle Main Engines, as they are the engines used in Space Shuttles. And they’re not just engines of the same model as the Space Shuttle, but the very engines that have been in space many times before, which have been in storage since 2011. The four engines for Artemis I have already been into space 3, 4, 6 and 12 times. Only minor modifications have been made, mainly modernizing the computer that controls them, increasing thermal protection because of the closer proximity of the boosters and increasing the power level – in the SLS, the engines will only be used once, so they don’t need to survive for reuse. After using up 16 of the engines inherited from the Space Shuttle, new RS-25Es will be used, also produced by Aerojet Rocketdyne, with a few more performance gains, which will take the low orbit capacity from 95 to 105 tons. The main stage was manufactured and assembled at NASA’s Michoud Assembly Facility in Louisiana, mainly by Boeing.
2. Solid Rocket Boosters (SRBs)
Also coming from the Space Shuttles are the two boosters, attached to the side of the main stage, which burn solid fuel. They are expanded versions, with 25% more thrust, by using 5 segments (instead of the 4 used for the Shuttle) and without having to carry the weight of the parachutes for recovery. They are mainly built with components that were used in the Shuttle program, for the first 8 flights (Block 1 and Block 1B). For Block 2, a new version will be used, currently under development by Northrop Grumman, with the main difference being that the structure will be lighter, made of composite materials instead of steel, which, together with the new second stage, will bring the mass capacity of the SLS Block 2 to 130 tons.
3. Interim Cryogenic Propulsion Stage
For the second stage, the first flights will use the Interim Cryogenic Propulsion Stage (ICPS), produced by Boeing, almost identical to the Delta Cryogenic Second Stage (DCSS) used in the Delta IV rocket since 2002, using liquid hydrogen and oxygen, with an RL10B-2 engine for the first flight and RL10C-2 for the next 2. Produced by Aerojet Rocketdyne – Pratt & Whitney, the RL-10’s origins lie in the 1960s, used on the Centaur A (second stage of the Titan rocket) and Saturn I. For SLS block 1B onwards, the entire second stage will be replaced by the Exploration Upper Stage (EUS), a larger version with more thrust, currently under development, which will have 4 RL-10C-3 engines, in the future replaced by RL10C-X. This second-stage change, along with the replacement of the SRBs, will increase the capacity of the SLS from 105 to 130 tons.
Orion Multi-Purpose Crew Vehicle
Strictly speaking, the last stage to be used in the Artemis missions, the Orion vehicle, is not part of the SLS – it is the cargo being carried by the SLS on these missions. But since it’s the third stage that we’ll see in use in these first missions, let’s talk about it here. In unmanned uses of the SLS, the Orion command and service modules would be replaced by another payload, such as the Europa Lander mission vehicle, which is still being formulated.
Designed for use on manned missions beyond low Earth orbit, the crew occupies a conical capsule, the Command Module (CM), built by Lockheed Martin, a larger, modernized version of the Apollo capsules, to carry typically 4 astronauts (up to 6), typically for 21 days, instead of the 3 Apollo astronauts for 14 days. The Command Module is the only part that enters the Earth’s atmosphere on the way back, landing on the ocean. The European Service Module (ESM), which is attached to it, contains an engine, fuel and oxidizer tanks (aerozine and dinitrogen tetroxide) and solar panels. This is an ESA contribution and is built by Airbus Defence and Space. The ESM’s AJ10 engine, produced by Aerojet Rocketdyne, also has a long history: versions of it have been used since the 1960s, including the Apollo service module and the Space Shuttle’s orbital maneuvering system, as well as various versions of Vanguard, Atlas, Thor and Titan. The engine used in Artemis I has already been in space on 19 Space Shuttle flights since 1984!
This figure shows that the capsule isn’t that much bigger and the service module is more compact, but the habitable volume is 50% larger, which is due to the reduction in the volume occupied by instruments and other equipment and to the fact that electricity is generated by solar panels – Apollo used fuel cells, which required large tanks for hydrogen and oxygen.

As detailed in our article on Artemis, in this program Orion will only be used as a vehicle to transit between the Earth and the Moon, as the astronauts will have much more space in the station that will be orbiting the Moon and in the permanent base on the surface.
This video shows the SLS assembly process for the Artemis I
Find out more at
Our article on the Artemis Program:
Official website: https://www.nasa.gov/exploration/systems/sls/index.html
This post is also available in:
Português